A Raymond maintient sa position parmi les leaders mondiaux dans sa spécialité, notamment en améliorant les processus d’assemblage chez ses clients.
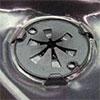
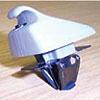
Différentes méthodes existent pour identifier les besoins de nos clients : les visites, le démontage et l’étude des produits et ce qu’on appelle les « Line Walks » (sorte de lignes directives établies par le FSP A Raymond et faisant partie intégrante d’une méthodologie complexe d’analyse des besoins clients, avec pour but la proposition de solutions en adéquation).
Les multiples « Line Walks » menées ces 3 dernières années chez différents clients tels que Audi, BMW, Ford, GM, Hyundai, Mercedes-Benz, Peugeot, Renault et Volkswagen, ont permis de perfectionner notre approche de préparation de ces « Line Walks », dans le but aussi bien de les exécuter que de les documenter de façon professionnelle. Nos clients ont été satisfaits des résultats de ces « Line Walks » et notre réputation dans l’industrie automobile s’est renforcée.
La méthode RayWalks vise à identifier les possibilités d’économies sur les lignes d’assemblage de nos clients. Ses objectifs sont les suivants :
- Elaborer une norme internationale d’exécution des Line Walks ;
- Assurer une préparation et une exécution correcte des Line Walks ;
- Mettre en place le service de support nécessaire pour le suivi des propositions ;
- Réaliser un guide destiné aux nouveaux participants à ces « Line Walks »;
- Améliorer la communication et la collaboration au sein du réseau ;
- Créer un réseau d’expertise ;
- Développer de nouvelles activités.
Chaque activité de « Line Walk » doit être gérée comme un projet.
Une « Line Walk » comprend différentes phases et étapes importantes.
Notre expérience de plusieurs « Line Walks » réalisées ces dernières années, a débouché sur l’élaboration d’ une check list améliorant la préparation projet, côté client, et mais aussi en interne. Il est essentiel pour le succès d’une « Line Walk » que la direction de l’usine – côté client - supervise les activités et soit parfaitement informée de l’étendue et de l’objectif de l’étude. Les réglementations sur la sécurité ont aussi leur importance ; elles doivent être parfaitement intégrées. Les photos sont le meilleur moyen de constituer cette documentation ; il est donc impératif d’avoir la possibilité de prendre des photos. Le client peut se charger de cette tâche ou nous en laisser la responsabilité par une autorisation officielle. Bien entendu, les ouvriers et le comité d’entreprise doivent également être informés des activités prévues et nous devons être autorisés à organiser des entrevues avec les ouvriers de la ligne d’assemblage.
Toute « Line Walk » débute par une réunion d’information avec tous les participants afin de recueillir les dernières informations sur les exigences de l’usine et les volumes de production réels. Il est utile qu’une salle soit disponible pour le travail de préparation lors des phases d’interruption de la ligne d’assemblage. Les principaux participants disposent d’une fiche de saisie assemblage (Assembly Record Sheet) tout au long de l’étude. Au terme de la « Line Walk » l’équipe doit retravailler cette fiche de synthèse Excel en tenant compte de toutes les propositions.
Le succès des « Line Walks » repose beaucoup sur le suivi des actions qui ont été validées.
Une méthode probante consiste à classer par ordre de priorité les différentes propositions et ce en étroire collaboration avec l’équipe adéquate côté client. Etablir une liste des 10 principales propositions est la meilleure façon de se concentrer sur les propositions ayant les meilleures chances d’êtres menées à bien. Une liste est également utile pour le suivi des propositions promettant des résultats rapides.
La méthode RayWalks est une méthode désormais approuvée pour identifier les économies potentielles chez le client.
Le gain résultant de cet exercice s’évalue à plusieurs millions d’euros par an pour le client d’un produit fabriqué en masse.
N’hésitez plus à nous contacter si vous pensez que nous pouvons vous aider à améliorer votre processus d’assemblage. contact.fr@araymond.com
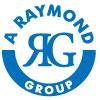