Few areas of a vehicle have to fulfill higher requirements than the underbody. Starting with the high temperatures close to the exhaust system, there are also special requirements like gravel impact, dust, sand and high humidity. So, for example the air deflectors at the wheel have to pass the curbstone test at -40°C and the lines for fuel and brakes are supposed to be fixed with clips giving noise damping characteristics. Poor road surfaces and high speeds lead to high impact possibilities and constant vibration stress.
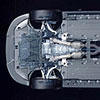
.
There are several areas of the underbody, starting with the heat shields, above this the brake- and fuel lines and finally the aerodynamic panels (Picture 1). Many different joining techniques are used such as screwing, welding, clipping, riveting and bonding, creating manufacturing complexity.
In addition to the requirement of fulfilling the functions throughout a vehicle's life, the joining techniques have to be designed in a way to guarantee a quick and process-sure assembly and to allow easy disassembly and reusability in case of repairs and recycling.
Advantages and disadvantages of the joining techniques on the basis of an underbody benchmark with 6 current vehicles
For a detailed analysis of the joining techniques, the following vehicles have been selected:
Audi A6, BMW series 1, BMW series 3, Ford C-Max, Peugeot 407 and Volvo V50
On tearing down the vehicles we have focussed the underbody modules:
- Engine encapsulation
- Heat shields
- Aerodynamic panels
- Wheel house liners
- Underbody air deflectors
- Lines for fuel / brakes / power steering
The diversity of variants is enormous, we found in a medium sized vehicle, 11 fastening methods with a total number of 179 fastening types.
For an evaluation of the different fastening methods, first of all we have investigated the requirements by surveying the OEMs and their Tier 1 suppliers. The requirements for the fastening of panels on the underbody are:
- Quick assembly
- Process sure assembly
- Low assembly forces
- Fastening elements pre-assembled with structural components
- Tolerance compensation +/- 2 mm
- Long lasting connections
- Robust fastening elements (gravel impact, abrasion, ...)
- Easy-to-maintain (easy opening / closing)
- Corrosion resistant /corrosion protected
Due to speed requirements, screwing was not considered as a quick assembly process. In contrast, screwing processes have advantages concerning process stability - unless they are operated with torque monitoring. The quarter-turn lock Fastener collected advantages for its quick and easy disassembly. As the lock is manually locked there is a devaluation concerning "quick assembly".
An example of Heat Shield Fixing
Several types of metal fastenings were found. A common type is a hexagon nut with collar screwed on a threaded weld stud. This is however more laborious than simply pushing on, can be robust if torque control is maintained and operator correctly assembles.
The A Raymond solution is a spring steel clip which is pre-assembled onto the heat shield and simply pushed onto the threaded weld stud with clamp pressure precisely maintained by elastic tongues. For disassembly the metal clip can be unscrewed. The A Raymond solution has advantages of pre-assembly on the shield, speed of assembly, and anti rattle in service (Picture 2).
An example of fastening of fuel- and brake lines on the underbody
The requirements to fastening correspond with those to the panels, in addition there is the demand of noise damping. If the fuel- and brake lines are covered by panels, the requirements regarding gravel impact and abrasion can be reduced.
For this purpose there are the following variants:
a) One component-plastic clip with elastic plastic tongues
Advantage: low-cost
Disadvantage: spring character of the plastic tongues is dropping
b) Metal clamp with TPE-Insert
Advantage: robust and good noise reduction
Disadvantage: not as low-cost as a)
c) 2-components plastic clip (hard / soft)
Advantage: good noise reduction
Disadvantage: hard shell is fracture susceptible (gravel impact, …..)
d) 1-component clip from structural
Advantage: robust, good noise reduction and low-cost
Disadvantage: none
Summary
Through our benchmark activity we have proved to OEM’s and Tier 1’s the benefit of our extensive intelligent fastening solutions.
The two successful examples highlighted in this article; Patented ARBAG material as a robust economic one piece solution (as opposed to bi injected or rubber inserts) giving advantages of noise damping with high impact resistance at all temperatures (ideal for fuel, brake, power steering, clips and aerodynamic spoilers).
Spring steel has a place too, it’s properties can be used to create intelligent fastening solutions such as the one piece easy push on screw off heat shield fixing.
For further information please contact us
contact.fr@araymond.com
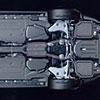
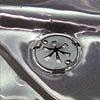