What are Ray-nice® and Ray-tool®?
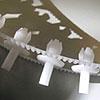
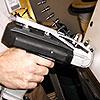
1) Are the Ray-Nice® and Ray-Tool® systems intended for particular applications on a vehicle? If yes, which ones.
The first application is to fix the inner layer of a bumper with plastic rivets. The serial production of the vehicle will start beginning of next year. There are several other applications possible with this system.
2) What are the cost advantages of the product and process? In what way is it an innovation? (Please explain the cost reduction aspects for the customer, which, if I believe your site, is very significant and can address current problems).
Injection moulded plastic fasteners are normally produced in bulk and delivered in high volume boxes to the customer.
Ray-nice® is a patented process to produce injection moulded Fasteners on a coil.
Nice stands for: Nonstop Injected Clip Equipment. It has been developed to reduce the “in place” process and logistic cost of plastic Fasteners. The parts are moulded in-line with transport straps of the same material (see picture).
Ray-nice® straps are designed like a toothed belt. This allows a very fast and precise application of the parts. After the parts are used, the straps can be 100% recycled. There is no waste material.
No special feeder is required to guide and separate the parts as there is for bulk material. The parts are 100% online quality controlled with 2 cameras which guarantees 0 ppm. This is ideal for use with an automated assembly gun.
We developed the Ray-Tool® gun for the rapid assembly of plastic rivets and other fasteners. This tool is electronically operated and its cycle time lasts less than 1 second. It can be used with either batteries or a power adapter.
Ray-tool can also be used with a robot; it is especially aimed at the processing of "endless" parts. The fixing of the assembly unit is done thanks to this robot arm. After the fasteners have been used, the rewinding of the transport straps onto a coil is automatic. Once they have been rewound, the straps are shredded, stocked and recycled.
3) What prompted the need for Ray-Nice® and Ray-Tool®? What precise problem do they address?
The general problem with fasteners is that 80% of the total “in place” cost can be attributed to the assembly process, logistics and overhead costs, only 20% of the total cost is the fastener piece price.
4) Did you make a particular effort to reduce the cycle time, which seems very fast?
The main advantages of processing the "endless`" parts with the Ray-tool® system and a robot - compared with other processing of bulk material - are the following :
A reduction of the 80% non-productive time by supplying the parts on an "endless” coil directly to the assembly head. This avoids the unproductive time for pick-and-place parts on the production line .
Even parts that cannot be fed - or that are fed with great difficulty - on conventional systems can thus be processed.
Considerably higher productivity due to a stable and unchanging process
5) It would also seem that you paid special attention to the feature of your solutions?
see answers above.
6) Can you explain to us, without revealing your secret, the development of the Ray-Nice® and Ray-Tool® solutions such as stemming of the R&D services of A Raymond?
Our approach to R&D to develop innovative systems for our Fastener business is always the same. We regularly perform benchmarks, teardowns and line-walks to find non-productive processes using fasteners at our customer’s assembly lines.
I always say to my team, if they see a time-consuming assembly problem at the customer’s plant, we are half way to an innovation.
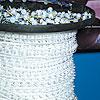